Comparative Study of Cost and Eco-Efficiency Factors of Aluminum and Conventional Formwork in The AYOMA Apartment Construction Project
DOI:
https://doi.org/10.24036/cived.v11i1.508Keywords:
Aluminium Formwork, Conventional Formwork, Cost Comparison, Eco-EfficiencyAbstract
The AYOMA Apartment construction project used two types of formwork; both aluminum formwork and conventional formwork are applied on one floor. A comparison of the costs of the two types of formwork used has not been carried out in the project planning. This study aimed to obtain a comparison between aluminum formwork and conventional formwork in terms of cost and eco-efficiency factors. The comparison was made specifically on the formwork of the 3rd Floor of the West Tower, The AYOMA Apartment. The unit price analysis of formwork was based on the coefficient of each work item following the regulation on Unit Price Analysis of Public Works and unit price standards applicable in the project location area. The eco-efficiency factors were calculated from the waste produced by manpower. The calculation results showed that the cost of aluminum formwork for the 3rd Floor of West Tower of The AYOMA Apartment is IDR 2,708,328,757.73 or 2.25 times higher than the conventional formwork cost of IDR 1,204,987,034.60. However, when the reusability factor was considered, aluminum formwork is up to 14.83 times more efficient than conventional formwork. In the eco-efficiency factors analysis, the waste produced by manpower for the work of aluminum formwork is less, only 56.48% of the waste produced by manpower for the work of conventional formwork. The amount of waste produced from the main material and the quality of concrete produced by using aluminum formwork support the conclusion that aluminum formwork is more eco-efficient than conventional formwork.
Downloads
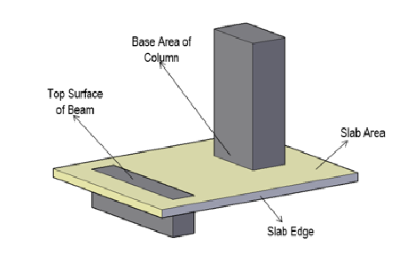